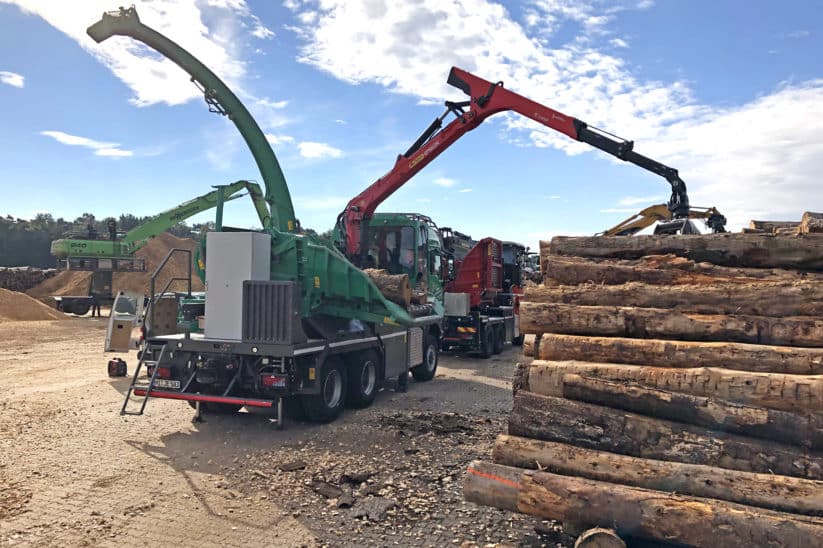
Die größte Herausforderung für einen Holzhacker ist die ständig variierende Belastung durch wechselnde Durchmesser oder Härten der Holzstämme, die zerkleinert werden. Die Motorleistung einer Maschine ist dabei auf die maximale Stammdicke ausgerichtet und für den Großteil der zu bearbeitenden Hölzer somit meist überdimensioniert. Dadurch verbrauchen die Hacker deutlich mehr Diesel als eigentlich benötigt. Das war die Ausgangslage für das Team des Labors für Baumaschinen an der Technischen Hochschule Köln. Die Forscher versuchten nun, dieses Problem durch den Einbau eines elektrischen Generators zu lösen. Der Dieselmotor verbleibt im Fahrzeug, treibt aber den Generator an und nicht wie bisher direkt die verschiedenen Komponenten des Hackers. Diese werden nämlich nun elektrisch durch den Generator versorgt. Das Konzept sah einen mittelstarken Dieselmotor vor, der nicht mehr so viel Leistung bringt, wie für die dicksten Stämme nötig wäre. Werden dünne Äste oder Gestrüpp verarbeitet, lädt die überschüssige Energie die Batterien auf. Diese unterstützen die Maschine, wenn Lastspitzen benötigt werden.
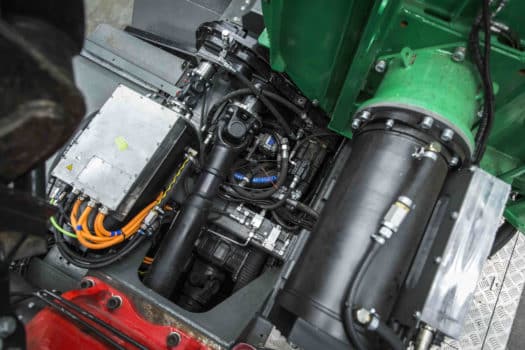
In einem ersten Schritt analysierte das Projektteam den aktuellen Aufbau der Maschine und erstellte ein virtuelles Modell. An diesem wurde das Energieeinsparpotenzial der einzelnen Komponenten untersucht. Darauf basierend überlegten sich die Forscher, wie man den Generator zwischen Dieselmotor und Maschine schalten kann. Zudem wurde eine neue Regelungsstrategie entwickelt. Bevor es mit einer realen Maschine in die Praxis ging, wurde das Konzept am Versuchsstand der Kooperationspartner (siehe Kasten) geprüft.
Elektromotoren ergänzen Verbrenner
Neben dem dieselbetriebenen Motor, der sowohl den LKW-Antrieb als auch das Hackaggregat mit Leistung versorgt, verfügt das Versuchsfahrzeug nun zusätzlich über drei Elektromotoren mit insgesamt rund 200 kW Leistung. Der Verbrenner-Motor läuft so während des Hackvorgangs möglichst nah an seinem optimalen Betriebspunkt. Wird für den Hackvorgang nur wenig Leistung benötigt – weil beispielsweise etwa gerade Kronenholz verarbeitet wird – lädt die überschüssige Energie dreizehn sogenannte Superkondensatoren auf. Diese speichern elektrische Energie und können sehr schnell ge- sowie entladen werden.
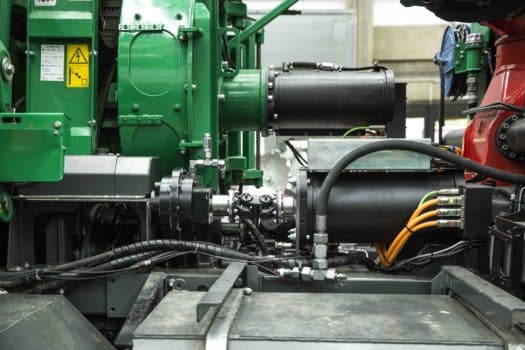
Benötigt das Zerhacken eines dicken Stamms mehr Leistung als der Verbrenner im optimalen Betriebspunkt bereitstellen kann, schalten die Elektromotoren in den sogenannten Boost-Modus und liefern durch das Entladen der Superkondensatoren die Differenzleistung zu. Der Boost-Modus springt automatisch an, wenn mehr Kraft gebraucht wird. Der Maschinenführer hat aber auch die Möglichkeit, den Boost manuell dazu zu schalten, um bestimmte Arbeitsprozesse zu beschleunigen.
Belegte Treibstoffersparnis
In einem finalen Test verglichen die Projektpartner ihren umgebauten Hacker mit einem baugleichen Modell mit herkömmlichem Antrieb. Als Testmaterial dienten Baumstämme vergleichbarer Härte, Durchmesser und Beschaffenheit. Insgesamt verarbeiteten die beiden Hacker während der Testphase rund 100 Festmeter Holz. Das umgebaute Modell verbrauchte dabei rund 20 % weniger Diesel bei gleicher Qualität der Hackschnitzel und gesteigerter Arbeitsleistung, bezogen auf die Hackschnitzel pro Zeiteinheit.

Das Forschungsprojekt „EnGie-Hacker“ des Kölner Labor für Baumaschinen an der dortigen Technischen Hochschule wurde im Rahmen der Initiative „EFRE.NRW“ in Zusammenarbeit mit dem Ministerium für Wirtschaft, Energie, Industrie, Mittelstand und Handwerk des Bundeslandes Nordrhein-Westfalen und dem europäischen Fonds für regionale Entwicklung der Europäischen Union gefördert. Das Projekt startete am 1. Januar 2017 und hatte eine Laufzeit von drei Jahren. Die Fördersumme für das Gesamtprojekt betrug rund 1,5 Mio. Euro. Beteiligt waren außerdem die Firmen Jenz Maschinen- und Fahrzeugbau GmbH, Roth Antriebstechnik GmbH und Vemac GmbH.
Kommentare